FDM FAQ’s
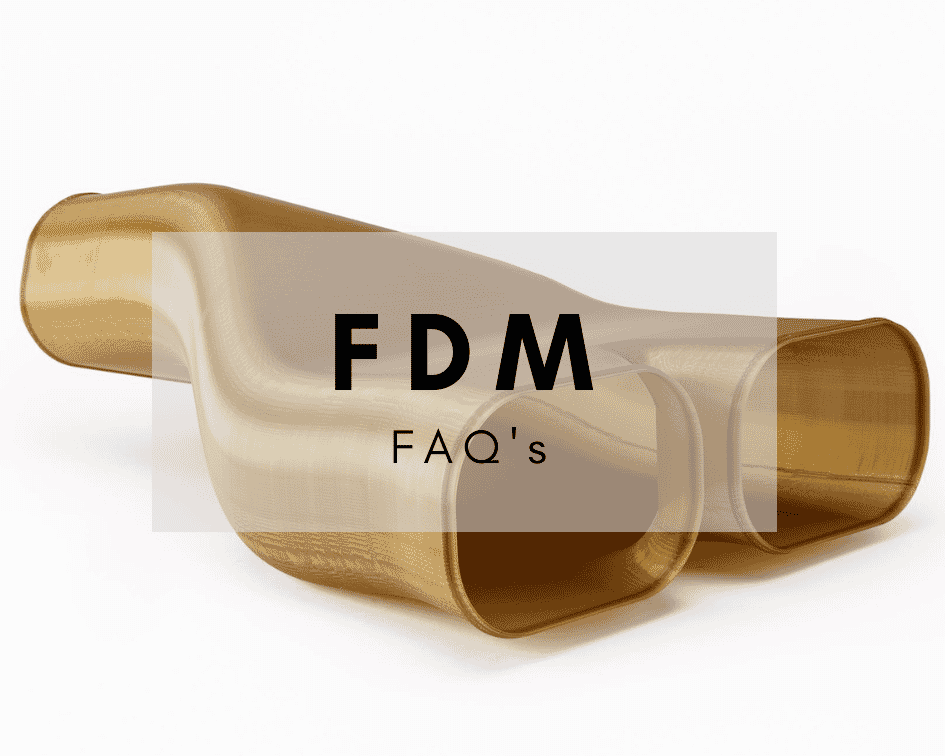
Our bureau manager answers all of your FAQ's on FDM technology...
How does FDM work?
A bead of Thermoplastic is extruded through a fine nozzle or tip at a high temperature so that molten plastic can be laid onto the print bed in contours. These contours are printed adjacent to each other to create solid features or in a ‘zig zag’ raster fill to generate the interior
Is there a minimum order charge for FDM printing?
Yes, we have a £50 minimum order charge for all technologies at 3DPB
What is the smallest wall thickness you can achieve with FDM?
Ideally 1.0 mm. We have printed less, but at 0.5 mm it isn’t possible to print using Stratasys FDM systems
What’s the biggest bed size you can print FDM on?
406 x 355 x 406 mm XYZ
What’s the best accuracy you can achieve with your FDM printers?
Parts are produced within an accuracy of ± .127 mm (± .005in.) or ± .0015 mm/mm (± .0015 in/in), whichever is greater.
What materials can you print in with FDM?
All Stratasys FDM materials with the exception of Nylon 6
We can print with ABS-M30, ABS-ASA, ABS-ESD7, PC, PC-ABS, Nylon 12, Nylon 12 CF, Ultem 9085 etc.
What colours are available with FDM?
There are many colours available including red, green, yellow, blue etc but most commonly black or white are used
Is FDM suitable for electronics applications?
The ABS-ESD7 material has static dissipative qualities making it ideal for environments where precision electronics or static shock are a risk
Are any of the FDM materials flame retardant?
Several FDM materials carry UL certification for flame retardancy
How strong are FDM models?
Different materials have different mechanical properties and we can provide data sheets to give this detail, but part strength is also affected by build orientation and the construction of the model. We can orientate a model to use the minimum amount of support material and therefore the lowest cost or use an orientation that will give best part or feature strength. The internal structure of an FDM model can be modified to create a tool path that adds strength to a particular feature or the whole part, but conversely density can be reduced by creating a honeycombed, sparse interior that reduces weight, material used, print time and cost.
Is FDM suited for the manufacturing floor?
Given the strength, accuracy and relative low cost of FDM materials they are perfect for many industrial applications such as jigs, fixtures, test beds, location tools etc
How is the support material removed from an FDM model?
There are two types of support material: soluble and non-soluble. Non-soluble support is used with the higher temperature materials such as Ultem 9085. This can restrict some parts to specific orientations to avoid support being generated in features where it is impossible to remove without machining. Some parts just can’t be printed with non-soluble support.
Soluble support is dissolved in a caustic solution. It is possible to print the whole part using soluble support material and this can be used to create sacrificial tools for production of carbon fibre components.
Can FDM models be smoothed and then painted?
There are a few options to create a high quality smooth surface with an FDM model, Vapour smoothing is possible with lower temperature ABS materials, Tumbling is possible for all materials and hand sanding can be used. Once primed and painted FDM models can be similar in appearance to an injection moulded part.
Is it true that you can print with Carbon filled Nylon on an FDM system?
Yes, we have recently become one of the few companies in the UK to have the Nylon 12 CF (Carbon Filled) upgrade to our Fortus 450mc.
What is the main limitation with 3D printing in FDM materials?
In terms of geometry, feature size can be limiting and surface quality due to its low definition. FDM models are porous and so aren’t suitable in their raw state for containing liquids.
In terms of production, FDM models do take quite a long time to print and print time is linear, meaning if you print two models it takes twice as long as one. This means that lead times can only be reduced by having more printers